Troubleshooting Guide
The root cause of most process-related failures in an anodize line is easy to identify and remedies are usually straightforward. For example: if the seal quality fails to dye spot stain, check the seal parameters; if the coating is too thin, check the anodize parameters. This discussion focuses on the more challenging yet fairly common defects and time-tested troubleshooting strategies used by today’s competent anodizer.
Troubleshooting Strategies
- Someone must take on the responsibility to solve the problem – take charge!
- Learn what you can: coating thickness, seal quality, defect frequency, appearance, type, shape, in/on/under the coating, location on the part, on the rack, alloy type, and source.
- Spend time on the line and discuss the problem with the operators. Critically assess their opinions and their performance. Take measurements of important process parameters.
- Call the experts and present all the information. Critically assess their opinions.
- Isolate the process step and the process parameter. Try to make one change at a time.
Notice
To our best knowledge, the information and recommendations contained herein are accurate and reliable. However, this information and our recommendations are furnished without warranty, representation, inducement, or license of any kind, including, but not limited to the implied warranties of merchantability and fitness for a particular use or purpose. Customers are encouraged to conduct their own tests and to read the product labels carefully before using them. Furthermore, the customer assumes sole liability for any patent infringement that occurs by reason of their following our recommendations or using the information given.
- Smut
- Stains
- White Spots
- Pits
- Etch Non-Uniformity
- Color Non-Uniformity
- Off-Color Dye Parts
- Burning
- Coating Adhesion
Common Defects: Smut
Smut is often seen on color work because it is easy to spot. Sometimes it presents itself as a powdery residue and other times as a black part with an iridescent green or blue cast. The color of the residue after wiping on a tissue can be a good clue as to the source, however, it may be prudent to use an isolation strategy to pinpoint where a process change needs to be made. The source of smut can usually be traced back to either of the following process steps.
Seal
This is usually the source. Ensure the pH isn’t too high. Hydrothermal sealing naturally causes smut, so proprietary chemicals are used for control. These chemicals do decompose over time, particularly when exposed to high-temperature surfaces, so seals have a natural life expectancy. The use of filtration combined with replenishment will extend life, but there will come a time when it is time to dump. This could be days for a hot water seal, weeks for a hot nickel acetate seal, months for a mid-temperature surfactant-based seal, or years for a cold seal.
Dye Bath
If the dye is new and the smut is isolated to this step, it may be a sign that the dye is overly active and a reduction in temperature may help to promote adsorption more deeply into the pores. It is more likely however that the dye bath has aged. Try dye bath filtration, buffer, and pH adjustment. A related “dye smut” problem is when isolated spots of dye particle precipitation occur. These particles may be prevalent on edges or machined or knurled surfaces and they can be easily wiped off the surface. This defect is typically related to chloride content in the dye bath. Sometimes buffering can help.
E-Color
Grey smut may be due to over-plating. Cut back on time, voltage, and modulation. Anodize conditions may need adjustment to increase the thickness and/or porosity of the coating. Easy-to-remove yellow or white smut isolated to this tank is likely due to the fall-out of tin salts onto the part surface. Better filtration may be the only course of action.
Anodize
Soft coatings are prone to produce smut, particularly on copper-containing alloys. Critically evaluate the anodize temperature and current density. The latter may be easier to do in retrospect by asking the lineman how long it took to anodize the part, measuring the coating thickness, and applying the 720 rule. It shouldn’t take 50 minutes to get a 0.25 mil coating!
De-Smut
Surprisingly, parts that are not well de-smutted can carry this smut all the way down the line. 6063 T52 is a good example. That tenacious silica-rich residue may appear to be gone, but appearances can be deceiving. Check the temperature (> 65°F) and chemistry. Make sure it is well agitated. You can boost the effectiveness with additives like nitrates, persulfates, and bifluorides.
Common Defects: Stains
Stains can be found on clear and color work. A useful strategy is to determine whether it is a surface stain (can be cleaned), imbedded in the coating (gone after CrO3/PO4 stripping), or on the aluminum surface (still seen after stripping). Determining this will narrow your focus. The shape and location of the stain can also be valuable information. There may be a correlation with how the part was racked.
On Surface
Often associated with rinsing downstream of anodize, particularly post seal. Make sure your rinse tanks are clean and being used.
In Coating
If the stain is in the coating, it may be metal related. Reprocess the part and see if it comes back. Sometimes thinner and softer coatings will mitigate this kind of metal problem. If the stain is in a black dyed coating, e.g. reddish stain near edges, the dye may be coming to the end of its useful life. Often this is associated with aluminum content in the dye. Running the dye pH too low may exacerbate this problem.
Under Coating
If under the coating the focus should be on the pre-treatment. The problem may be scale not being removed before etch (try de-smutting before etching). It could be etch transfer staining (lower the etch activity and speed up the transfer). The stain may be due to poor storage conditions of the metal before it arrived on your floor (often the shape of the stain is a dead giveaway).
Common Defects: White Spots
White spots are often found on colored work. The shape (round, irregular) and location of the spots are good clues.
Round
Could be due to the metal e.g. Jig plate, Mic 6, Castings. Best course is to include a neutralization rinse after anodizing. White spots are often due to foreign particles from the air or rinse adhering to the coating and acting like a mask in the color bath. Etch mist in the air can be at fault, or mould particles in the post anodize rinse. Often a white spot is actually a popped blister and no coating is present at all (this should be checked). Blisters of this kind are usually metal related but they can be due to an interruption in the anodizing power. Blisters on electrolytic color (usually cobalt and nickel) can be due to high coloring voltages, and bath contaminants.
Irregular
These are most often due to pits or micro-folds in the aluminum that entrap anodize acid and slowly release it in the dye bath. The usual practice is to focus on rinsing after anodize. You could try a warm rinse, a nitric rinse, a neutralization rinse, or any combination.
Common Defects: Pits
Pits can take on a variety of shapes and forms and can be caused by metal quality, the environment the parts were exposed to while they were stored before processing, excessive chlorides in process tanks, bottlenecks resulting in extended immersion in rinse, stray currents and galvanic effects, soft anodize, inadequate cleaning (bright dip), etc. It is important to look at the shape of the pit, how they are arranged or distributed on the part, and to determine whether all parts on a load are affected. Another useful exercise is to determine whether a coating is present at the pit location.
Shape
Shallow “star” shaped pits over entire surface suggests chlorides in the anodize bath or corrosion occurring in the desmut rinse. Moat and castle shaped pits on bright work may be due to poor cleaning or aluminum phosphate precipitation (icing) on the part in the bright dip.
Arrangement / Distribution
Pits following the metal grain or extrusion direction may be caused by particles in the metal. Pits that are distributed over the entire part are likely caused by the finishing process. Galvanic effects, rinse tank staging, chlorides, etc. Fingerprint, spacer bar, one side only – these kinds of arrangements suggest the origin was in the handling or storage of the part before it got to the anodize line. If only a few randomly located parts on a load have pits, the source is likely related to the metal quality.
Coating Present
If the pit has a protective coating then you can assume that the pit originated before the anodize step. The reverse also holds true.
Common Defects: Etch Non-Uniformity
Both chemistry and metal quality can affect gloss uniformity. It is common to see banding on flat and curved surfaces along extrusion weld lines and opposite flanges. Visible ridges or die lines are also common. Occasionally the etched surface takes on a grainy, or galvanized appearance. All these defects are due to metal quality and/or extrusion practices. Some proprietary etch chemistries are more forgiving to these metal issues than others and are therefore worth trying, but as a general rule, a slower etch with the highest possible content of aluminum will give better results than a more aggressive etch.
Etch transfer staining is covered under Stains.
Common Defects: Color Non-Uniformity
Streaks and spots that may be partially colored can sometimes be found on individual parts and sometimes they can relate to the parts position on a load.
Non-Uniform Part
The color of individual parts may be mottled or have streaks. This is likely due to inadequate rinsing which may be exacerbated by high aluminum content in the anodize acid. It may be time to decant the anodize bath. Improved rinsing practices may include warm water and nitric conditioning. Foreign matter in the dye tank (oil, mold, etc.) can be the cause of spots or streaks that are partially colored and maybe even white looking. Inadequate cleaning can also result in an anodized coating that is partially masked and poor to pick up dye.
Non-Uniform Load
The color of parts on a load may not match up. Most often this is the result of coating thickness variations within the load. Ensure that the parts are well distributed in the anodize tank and that the anodizing is not done too quickly. Better to take 45 minutes to reach 0.7 mil rather than 25 minutes. Another cause of this problem may be too short of a dye time. The lower racked parts are immersed a few seconds shorter than the upper, and this may play a role if the dye time is only 30 seconds in all.
E-Color Parts
Mottled e-color may be due to insufficient dwell time before initiation of the electrical program. Lighter color in deep recesses is normal, but the variation can be minimized by adjusting the chemistry and/or electrical program. Parts should be racked so that they do not shield one another from the electrodes and they should be well distributed along the length/depth of the tank. Accelerated anodizing can cause coating softness near the contacts and corners, which can ultimately result in color variation.
E-Color Load
The entire perimeter of a load may be darker or sometimes lighter in color. If this is the case, and you are satisfied that the anodize process is reasonable, then look to the electrical program for coloring. The voltage may need to be reduced a little. If modulated, you may need to cut back on the bias. Make sure that the thysistors are in good working order.
Common Defects: Off-Color Dye Parts
Off-Color Dye Parts can usually be attributed to the dye bath. Your green may be too yellow or your grey too green, but sometimes the alloy/anodize or pretreatment creates the problem.
Alloy/Anodize
Some alloys (e.g. 7XXX) produce coatings that have a natural color that may interfere with targeting process. Alloy effects are exacerbated with accelerated anodizing treatments. Those who attempt to dye “additive” hard coat parts are particularly susceptible to this problem.
Pre-Treatment
The more notable pretreatments that interfere with color targeting are shot blasting and acid etching. Both create very low gloss finishes which tends to darken the color hue. Shot blasting can be irregular and this irregularity oftentimes doesn’t show up until the part is processed.
Dye Bath
Over time and use a dye bath may begin to change color. In the case of a black it may revert to its bluish or reddish base color. This usually means the bath has been depleted and/or contaminated. In other cases the color change may be due to decomposition of the dye bath. Some dyes are sensitive to high temperature operation. Other dye baths are multi-component where one component may exhaust faster, fall out of solution, or be more sensitive to contaminants or mould. Because no two dyes are alike, it is good practice to read the data sheet and talk to your chemical vendor for suggested practices.
Common Defects: Burning
Burning can take on different degrees of severity. It can be a softer coating near the contact point that may not even be noticeable or it can be a part that has completely disintegrated in the anodize tank. Burning is usually associated with one or more of: the alloy, the electrical contact, or the anodize process conditions. Alloy: High copper alloys are certainly the most likely to burn. It is counterintuitive that for a given ASF the voltage required for 2XXX alloys is far higher than others. More heat is generated at the base of the coating, and the likelihood is higher for small asperities to form in the barrier layer. These conditions favor a catastrophic highly localized chain of events – a burn. As a result, great care must be taken when processing these alloys.
Electrical Contact
To avoid burning you must avoid localized heating and this can occur where there is too much electrical current flowing through a point contact. The rule of thumb is for aluminum racks < 20A per contact and for titanium racks < 8A per contact.
Anodize Process
A number of variables need to be considered. The bath temperature needs to be controlled (lower is better), and the agitation needs to be adequate, if not vigorous. Conductivity of the bath plays a role, and it is better to use higher acid concentrations rather than lower. Higher aluminum contents have a negative impact on conductivity. Additives, such as the Reynolds MAE have been shown to reduce the potential for a burn to occur. Power to the part plays an important role. Higher current densities favor burning. The initial ramp rate or step-ramp program may require tuning. Pulse power systems are claimed to be the superior choice over standard DC.
Common Defects: Coating Adhesion
Coating Adhesion problems range from white spots (small popped blisters) to “feathering” at cut edges, to massive loss of coating. Many shops see this effect on heat-treatable alloys; 7075 and to a lesser extent 6061. It can occur on Type II and Type III finishes. The root source is likely metallurgical with current theory suggesting an accumulation of intermetallic particles with possible coprecipitated hydrogen occurring at the aluminum/oxide interface. Unfortunately for the anodizer, a universal processing solution has yet to present itself. Some have suggested anodizing with low-frequency pulsed power where, during the recovery phase, the barrier oxide can more easily accommodate these unwieldy particles. Others have found that their rectifier had unexpectedly high levels of ripple, and by addressing this they eliminated their problem. Others suggest that extending the voltage ramp for unusually long periods of time will reduce the unwanted effect.
Blistering can occur for other reasons as well. Anodizing stops and re-starts can be at fault for massive coating loss. A host of poor extrusion practices can cause subsurface pockets or blisters that are uncovered during anodizing. Unusually large unwanted iron phase particles (see photo) can fracture the coating. And for parts that are colored using the so-called “2-Step” method, an adjustment to the coloring power will usually remedy the problem.
Example of blistering
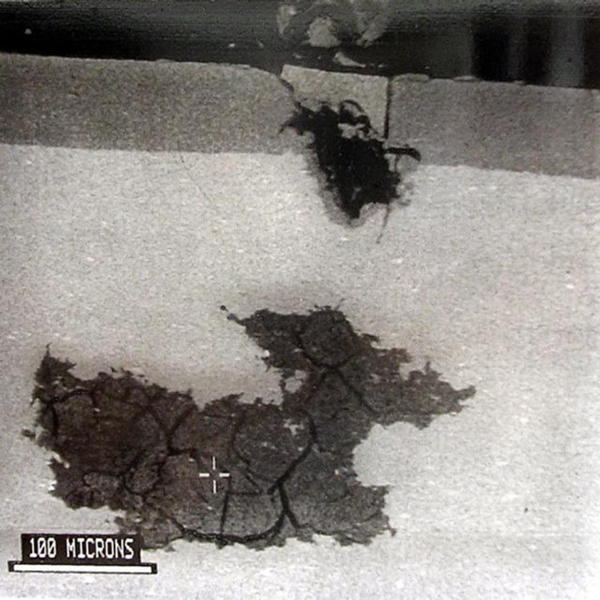